Anodic Coating Specifications
Suggested Specifications & Quality Control
The aluminum anodizing industry has established the following standards and guidelines for specifiers selecting anodized finishes:
Since color disparities can arise due to individual interpretations of named colors, it is vital that precise understandings of color and appearance be established for each anodizing project. The appearance of an anodized finish is influenced by more than depth of color. These other factors include alloy, temper, gloss, surface structure and the coloring process used.
The variety of aluminum materials and products incorporated into anodizing projects require that anacceptable range be agreed upon between the specifier-buyer and the manufacturer-anodizer on a
per-project basis.
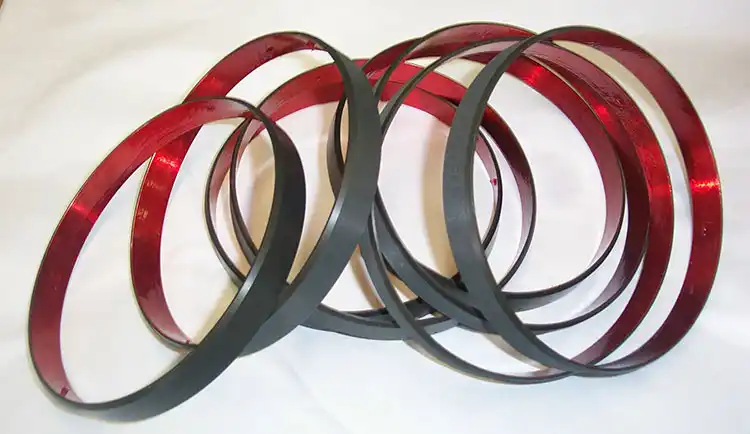
Detailed information on the various processes, tests and quality control systems referred to here can be obtained from the Aluminum Association (AA), the Aluminum Anodizers Council (AAC), and individual anodizing companies or other trade organizations.
Suggested anodizing specifications and quality control procedures:
Finish: All exposed surfaces should receive an architectural anodized finish in conformance with AAMA 611 standard. Processing should be sulfuric acid or equivalent anodizing with electrolytic or immersion deposited inorganic pigmentation in the coating. The resulting anodized finish should be continuous, fully sealed and free of powdery surfaces, smut and blemishes.
Alloys: All aluminum should be Aluminum Association alloys as recommended by manufacturers for the use intended and required to produce the specified finish.
The AAC Color Standards detail the specific testing procedure for anodic coating thickness, coating density and seal integrity. These properties can be checked by the appropriate ASTM B244, ASTM B137, ASTM B680, ISO 2360, or ISO 3210.
The anodizer is responsible for the quality control, including inspection and records of inspection, which are available to the customer upon request.